Presented By: Aerospace Engineering
Chair's Distinguished Lecture: Advanced Manufacturing of Aerospace Composite Structures: Predicting Influence of Imperfections on Composite Material Performance.
Paul Davidson, Assistant Research Scientist, Aerospace Engineering, University of Michigan
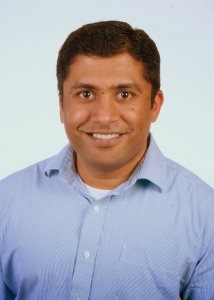
Paul Davidson
Assistant Research Scientist
Aerospace Engineering
University of Michigan
A review of future ideas for commercial aviation points towards four kinds of aircraft designs: high aspect ratio wing (HARW), blended body, Urban Air Mobility (UAM), and supersonic vehicles. From a structural perspective, these aircraft designs necessitate the use of advanced composites and manufacturing methods. Robotic systems like Automated Fiber Placement (AFP) technology for laying down composite material, offers one such manufacturing method, to address the future aviation needs. Even with advancements made in AFP technology, there are issues still plaguing composite manufacturing, namely imperfections. Imperfections refer to deviation from design intent and have ramifications on the performance of the structure. The identification of imperfections and subsequent rework/reject decision consumes about 20% of the total production time and is inconsistent. These inconsistencies in inspection and manufacturing are indirectly accounted for in a design, by increasing safety factors, thereby increasing the weight and cost of a structure.
In this talk, an overview of the challenges posed in the manufacturing of composite structures, as well as a framework to study the effect of manufacturing imperfections on material performance, will be presented. An experimental-computational framework that utilizes a small number of controlled defect coupon tests to develop a validated high-fidelity finite element model will be described. The framework utilizes Kriging regression, Support Vector Classification, and analysis using the Monte Carlo method to determine the risk of defects on the composites. To conclude, I will outline current research problems and opportunities for cross-collaboration between researchers in the areas of structures, materials, NDI, robotics, and data sciences.
About the speaker...
Dr. Davidson is an Assistant Research Scientist in Department of Aerospace Engineering at the University of Michigan, Ann Arbor. He received his MS and PhD degrees from the University of Michigan. From May 2016 to August 2018 he was a Post Doctoral Research Associate in the Composite Structures Lab of the Aero& Astro Department at the University of Washington, Seattle. From May 2013 to October 2015 he worked in the Composite Design and Analysis Lab of General Electric’s Global Research Center. He is also a member of the American Institute of Aeronautics and Astronautics (AIAA) Materials Technical Committee, and the vice-chair of Durability and Damage Tolerance (DaDT) Division of American Society of Composites (ASC). His primary research interests include composite mechanics, specifically on the damage, failure and fatigue of composite materials, advanced manufacturing methods, multi-scale analysis, low velocity and high velocity impact damage, and micro-mechanics.
Assistant Research Scientist
Aerospace Engineering
University of Michigan
A review of future ideas for commercial aviation points towards four kinds of aircraft designs: high aspect ratio wing (HARW), blended body, Urban Air Mobility (UAM), and supersonic vehicles. From a structural perspective, these aircraft designs necessitate the use of advanced composites and manufacturing methods. Robotic systems like Automated Fiber Placement (AFP) technology for laying down composite material, offers one such manufacturing method, to address the future aviation needs. Even with advancements made in AFP technology, there are issues still plaguing composite manufacturing, namely imperfections. Imperfections refer to deviation from design intent and have ramifications on the performance of the structure. The identification of imperfections and subsequent rework/reject decision consumes about 20% of the total production time and is inconsistent. These inconsistencies in inspection and manufacturing are indirectly accounted for in a design, by increasing safety factors, thereby increasing the weight and cost of a structure.
In this talk, an overview of the challenges posed in the manufacturing of composite structures, as well as a framework to study the effect of manufacturing imperfections on material performance, will be presented. An experimental-computational framework that utilizes a small number of controlled defect coupon tests to develop a validated high-fidelity finite element model will be described. The framework utilizes Kriging regression, Support Vector Classification, and analysis using the Monte Carlo method to determine the risk of defects on the composites. To conclude, I will outline current research problems and opportunities for cross-collaboration between researchers in the areas of structures, materials, NDI, robotics, and data sciences.
About the speaker...
Dr. Davidson is an Assistant Research Scientist in Department of Aerospace Engineering at the University of Michigan, Ann Arbor. He received his MS and PhD degrees from the University of Michigan. From May 2016 to August 2018 he was a Post Doctoral Research Associate in the Composite Structures Lab of the Aero& Astro Department at the University of Washington, Seattle. From May 2013 to October 2015 he worked in the Composite Design and Analysis Lab of General Electric’s Global Research Center. He is also a member of the American Institute of Aeronautics and Astronautics (AIAA) Materials Technical Committee, and the vice-chair of Durability and Damage Tolerance (DaDT) Division of American Society of Composites (ASC). His primary research interests include composite mechanics, specifically on the damage, failure and fatigue of composite materials, advanced manufacturing methods, multi-scale analysis, low velocity and high velocity impact damage, and micro-mechanics.